Wholesale flanges play an indispensable role in a variety of industrial applications, providing essential connections in piping systems across sectors such as oil and gas, chemical processing, and wastewater management. Understanding the different wholesale types of flanges available, their specific applications, and the benefits they offer can significantly enhance the procurement strategy for businesses seeking to optimize their supply chain and ensure high-quality outcomes.

Flanges are critical components used to connect pipes, valves, pumps, and other equipment to form a robust pipeline. They provide ease of access for cleaning, inspection, or modification, making them a preferred choice for engineers and procurement specialists. The wholesale market is rich with several types of flanges, each designed to cater to different needs and operational conditions, ensuring the demands of complex projects are met with precision.
A significant advantage of sourcing flanges wholesale is the cost-effectiveness it offers. Bulk purchasing minimizes per-unit cost, an essential consideration for large-scale operations. Additionally, wholesalers often offer a broader range of products, enabling buyers to select precisely the type of flange that meets their specifications without the requirement for custom manufacturing.
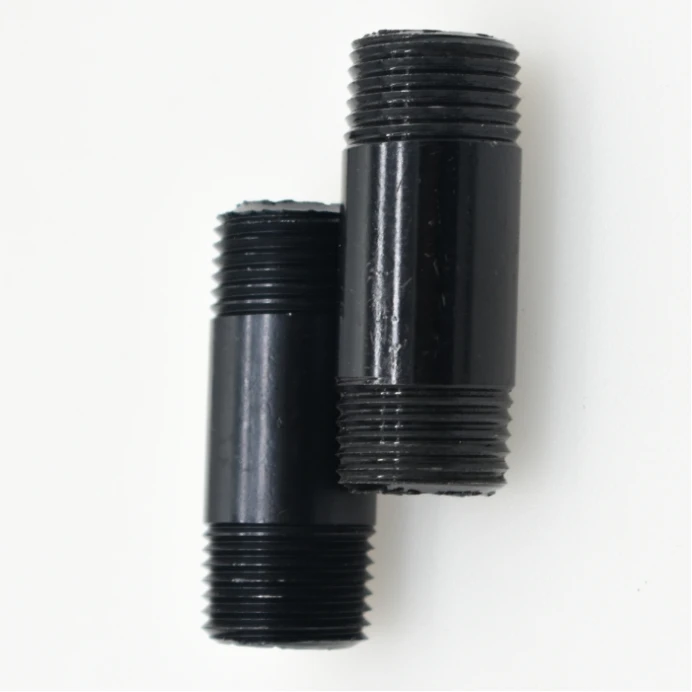
One of the most popular types of wholesale flanges is the slip-on flange. Its simple design and ease of installation make it suitable for many low-pressure applications. Slip-on flanges are preferred in scenarios where speed and efficiency are paramount, such as in water treatment plants or in emergency repair situations. The ability to slide the flange over the pipe simplifies alignment and attachment, reducing labor costs and installation time.
Weld neck flanges, another prevalent category, provide superior strength and are ideal for high-pressure environments. These flanges are designed with a long tapered hub that enhances stability and reduces the risk of leakage by providing an extensive surface area for welding. In the realm of chemical processing or any operation involving hazardous substances, the secure connection offered by weld neck flanges can be critical to operational safety and efficiency.
Blind flanges, which are used to close off piping systems, are essential for maintenance, testing, and repair operations. Their robust design makes them suitable for high-pressure environments or applications requiring complete termination of flow. Industries where pipeline isolation is frequent will find blind flanges indispensable, ensuring that the system integrity remains uncompromised during operational downtime.
wholesale type of flange
Another notable type is the threaded flange, which does not require welding. Ideal for environments where flange alignment may be altered post-installation, threaded flanges serve oil drilling and waterworks industries. Their ease of assembly and disassembly makes them desirable for applications requiring frequent adjustments or maintenance.
The lap joint flange, used in conjunction with a stub end, provides excellent flexibility for assembly and alignment. Suitable for systems requiring frequent disassembly, this type is particularly beneficial in industries such as petrochemicals and fertilizers where pipeline modifications are common.
Flanges, irrespective of the type, must meet specific standards and certifications to ensure their compatibility and performance in diverse environments. Organizations like the American Society of Mechanical Engineers (ASME) and the American Petroleum Institute (API) stipulate extensive regulations, ensuring that flanges can withstand various pressure ratings and temperature ranges, a crucial factor for industries dealing with volatile substances.
Establishing a partnership with reputable wholesale flange suppliers can drastically improve overall project outcomes. Such suppliers not only provide quality products but also expert advice and after-sales service, essential for maintaining the durability and efficiency of the installed systems.
Trust in flange sourcing can significantly impact business operations, making due diligence and supplier vetting crucial steps in the procurement process. Detailed quality checks, certification verifications, and supplier reviews ensure that the flanges not only meet operational criteria but also contribute to the long-term reliability of engineering projects.
In conclusion, while choosing the right type of flange from a wholesaler requires understanding specific application needs, the relationship with the supplier, and the necessary compliance standards. Businesses standing on this pivotal choice can ensure successful project execution by leveraging the expertise of seasoned suppliers and selecting flanges that align with their operational goals while remaining cost-effective.