The Artisanal Craft of Cast Iron Nipple Manufacturing
Cast iron, a material known for its durability and strength, has been a staple in manufacturing for centuries. One particular product that showcases the prowess of this material is the cast iron nipple, an essential component in various industrial applications, particularly in plumbing and pipe systems. This article delves into the world of cast iron nipple manufacturers, highlighting their craftsmanship, production processes, and the importance of their work.
A cast iron nipple, also referred to as a pipe fitting, is a short, straight pipe used to connect two lengths of pipe or to connect a pipe to a fitting. Its robust construction makes it ideal for high-pressure applications where reliability and endurance are paramount. Manufacturers of cast iron nipples are specialists in creating these vital connectors with precision and care.
The manufacturing process of a cast iron nipple begins with the selection of high-quality raw materials. Cast iron, composed mainly of iron, carbon, and silicon, is chosen for its excellent wear resistance and heat retention properties. The metal is melted in a furnace, a process that requires skilled supervision to ensure the right composition and temperature.
Once the molten iron is ready, it is poured into molds, which form the shape of the nipple. This step, known as casting, is a critical part of the process, as it determines the final dimensions and quality of the product. The molds are typically made from sand, clay, or a combination, and they must be carefully designed to allow for smooth casting and easy removal of the finished product.
After cooling, the cast iron nipples go through a series of rigorous inspections and finishing processes
After cooling, the cast iron nipples go through a series of rigorous inspections and finishing processes
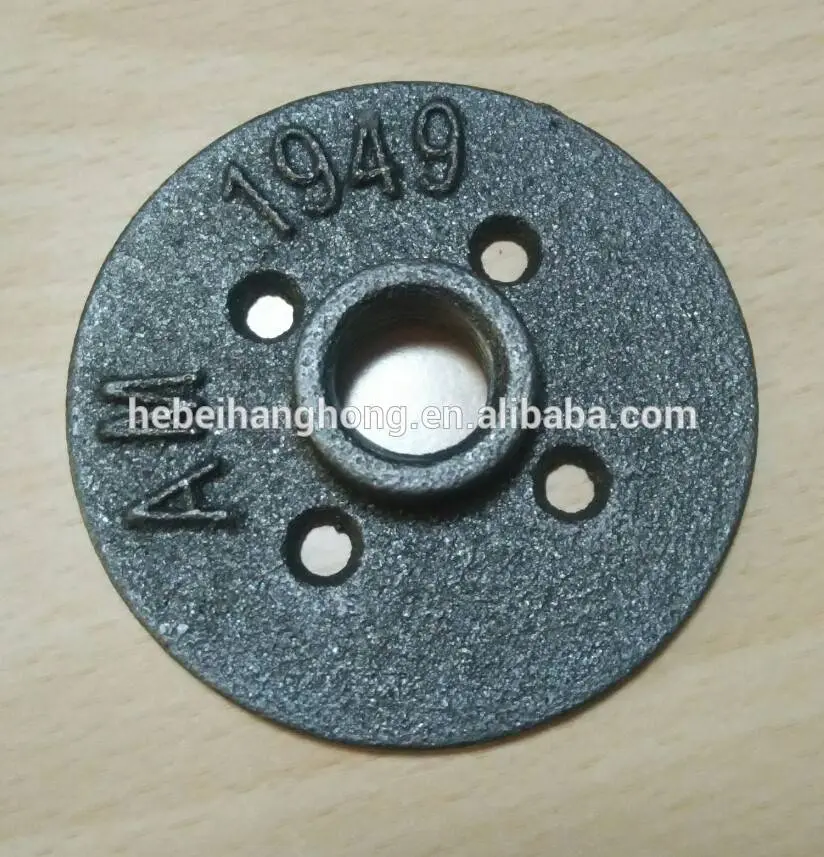
After cooling, the cast iron nipples go through a series of rigorous inspections and finishing processes
After cooling, the cast iron nipples go through a series of rigorous inspections and finishing processes
cast iron nipple manufacturers. These include machining, which refines the surface finish and ensures precise threading for seamless pipe connections. The nipples may also undergo heat treatment to enhance their strength and stability, followed by a coating process to protect against corrosion.
Manufacturers of cast iron nipples are not just producers; they are engineers, artisans, and problem solvers. They understand the nuances of the material and the demands of the industries they serve. Their expertise lies not only in the technical aspects of production but also in adapting to changing industry standards and customer requirements.
In today's fast-paced world, the role of cast iron nipple manufacturers is more crucial than ever. As environmental concerns grow, the use of durable and recyclable materials like cast iron becomes increasingly important. Furthermore, the need for reliable infrastructure in sectors like oil and gas, water supply, and waste management underscores the significance of their work.
In conclusion, the manufacture of cast iron nipples is a testament to human ingenuity and the enduring value of traditional manufacturing techniques. It combines age-old craftsmanship with modern technology, ensuring that these essential components continue to serve their purpose in countless industrial applications worldwide. The dedication and skill of cast iron nipple manufacturers play a vital role in maintaining the integrity and functionality of our global infrastructure.