Understanding Galvanized Threaded Nipples The Heart of Industrial Plumbing from the Factory Perspective
In the world of industrial plumbing and pipe fittings, one component that stands out for its durability and resilience is the galvanized threaded nipple. A vital piece in the puzzle of efficient fluid transportation systems, galvanized threaded nipples are manufactured in specialized factories, each unit embodying a fusion of precision engineering and robust material science.
A galvanized threaded nipple, simply put, is a short length of pipe with male threads on both ends, designed to connect two female-threaded pipes or fittings. The process of galvanization involves coating the steel nipple with a layer of zinc, offering it exceptional resistance against corrosion and rust. This makes it ideal for outdoor applications or areas prone to moisture, ensuring a longer lifespan and reduced maintenance costs.
The manufacturing process in a galvanized threaded nipple factory begins with the selection of high-quality carbon steel. The raw materials are then cut to the required length and machined to form the threads. These threads are meticulously crafted to meet industry standards, ensuring a tight and secure fit when connected to other fittings.
Once the threading is complete, the nipples enter the galvanization phase. Here, they are submerged in a bath of molten zinc. The zinc reacts with the iron in the steel, forming a metallurgic bond that creates a protective layer over the surface The zinc reacts with the iron in the steel, forming a metallurgic bond that creates a protective layer over the surface
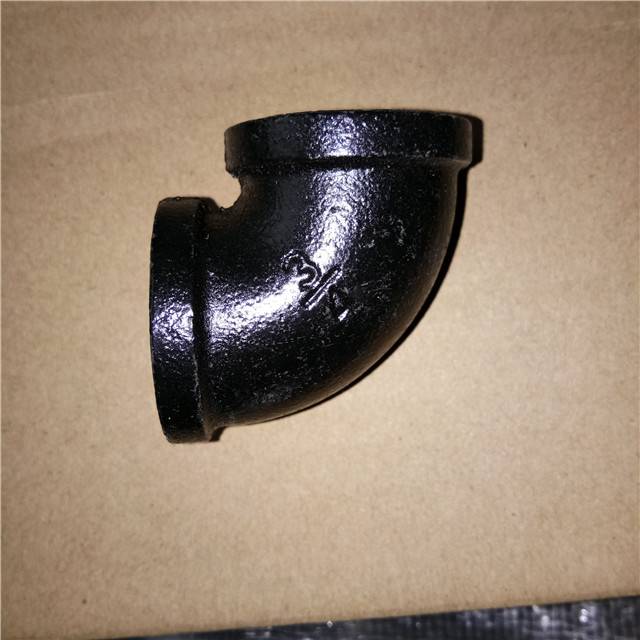
The zinc reacts with the iron in the steel, forming a metallurgic bond that creates a protective layer over the surface The zinc reacts with the iron in the steel, forming a metallurgic bond that creates a protective layer over the surface
galvanized threaded nipple factory. This process, known as hot-dip galvanizing, not only coats the exterior but also penetrates the small crevices and threads, providing comprehensive protection.
Quality control is paramount in a galvanized threaded nipple factory. Each batch undergoes rigorous testing to ensure the threads are damage-free, the zinc coating is uniform, and the overall dimensions meet the specified tolerances. Non-destructive tests like hydrostatic pressure testing may also be conducted to verify the integrity of the product under extreme conditions.
Moreover, these factories often cater to custom requirements, producing nipples in various lengths and thread sizes to suit specific industrial applications. From water supply systems to oil refineries, galvanized threaded nipples find their utility across a wide spectrum of industries.
In conclusion, a galvanized threaded nipple factory is more than just a production facility; it's a hub of innovation where technology, material science, and precision engineering converge. It's where the humble threaded nipple, fortified by zinc, transforms into a reliable workhorse of industrial piping systems, ensuring seamless flow and enduring performance. The importance of these factories lies not just in the products they manufacture but in the critical role they play in maintaining the operational efficiency of countless industries worldwide.