Malleable Iron Nipple Factories Revolutionizing the Industry
In the realm of manufacturing, malleable iron nipples have long been a staple, used in a myriad of applications due to their unique properties. These components, typically made from ductile iron, offer excellent strength and durability, making them ideal for use in high-pressure environments. However, the traditional methods of producing these nipples have been labor-intensive and time-consuming, leading to increased costs and reduced efficiency.
Fortunately, a revolution is underway in the malleable iron nipple industry, thanks to the advent of advanced manufacturing techniques. These new methods not only streamline the production process but also improve the quality and consistency of the final product.
One such technique is the use of CNC (Computer Numerical Control) machines. These state-of-the-art tools allow manufacturers to precisely control every aspect of the nipple-making process, from cutting to shaping to finishing. This level of precision results in nipples that are far more uniform in size and shape, which is essential for ensuring proper fit and function in their intended applications.
Another game-changer is the introduction of 3D printing technology. While still in its early stages, 3D printing has the potential to revolutionize the way malleable iron nipples are produced While still in its early stages, 3D printing has the potential to revolutionize the way malleable iron nipples are produced
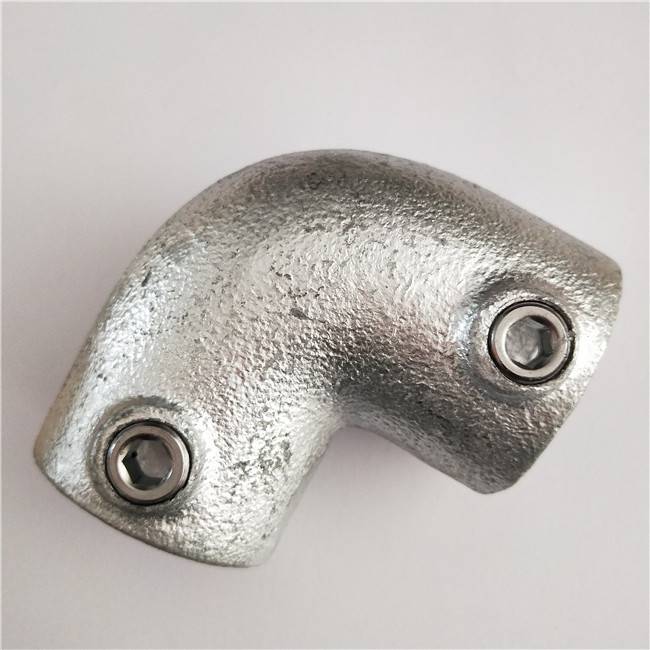
While still in its early stages, 3D printing has the potential to revolutionize the way malleable iron nipples are produced While still in its early stages, 3D printing has the potential to revolutionize the way malleable iron nipples are produced
malleable iron nipple factories. By using digital models, manufacturers can create complex geometries and intricate designs that would be impossible using traditional methods. This opens up new possibilities for custom nipples that are tailored to specific customer requirements.
Perhaps most significantly, these advances in manufacturing technology are leading to significant cost savings for businesses. By reducing the amount of manual labor required and increasing productivity, manufacturers can produce malleable iron nipples at a lower cost per unit. This, in turn, allows them to offer more competitive prices to their customers, while still maintaining high levels of quality and performance.
In conclusion, the malleable iron nipple factories of tomorrow are poised to be far more efficient, effective, and innovative than those of today. With the adoption of advanced manufacturing techniques like CNC machining and 3D printing, manufacturers can produce high-quality nipples at a lower cost, while also meeting the growing demand for customized solutions. As this revolution continues to unfold, we can expect to see even more exciting developments in the world of malleable iron nipples.