Understanding Flange DN20 Factory Production A Comprehensive Overview
In the world of industrial piping systems, flanges play a crucial role in connecting pipes, valves, and other equipment. One specific type that frequently emerges in various applications is the DN20 flange. This article delves into the manufacturing process at a flange DN20 factory, highlighting the importance of precision, quality control, and adherence to industry standards.
DN20, derived from the French Diamètre Nominal, refers to the nominal diameter of a pipe or fitting, which in this case is 20 millimeters. Flanges with this dimension are commonly used in medium-sized piping systems where a secure and reliable connection is essential. They are manufactured in factories that specialize in producing these vital components, ensuring a consistent supply for various industries such as oil and gas, chemical processing, and water treatment.
The production process at a flange DN20 factory begins with the selection of raw materials. High-quality carbon steel, stainless steel, or alloy steel, depending on the application's requirements, is chosen. The material is then cut into the desired shape using either laser cutting or CNC (Computer Numerical Control) machines, ensuring precise dimensions and smooth edges.
Once the blank is formed, it undergoes forging, a process that involves heating the metal to high temperatures and shaping it under immense pressure. Forging strengthens the material, enhancing its durability and resistance to stress. After forging, the flange is cooled and then machined to achieve the final dimensions and surface finish. This step is critical, as it ensures the flange's compatibility with mating parts and meets the required tolerances This step is critical, as it ensures the flange's compatibility with mating parts and meets the required tolerances
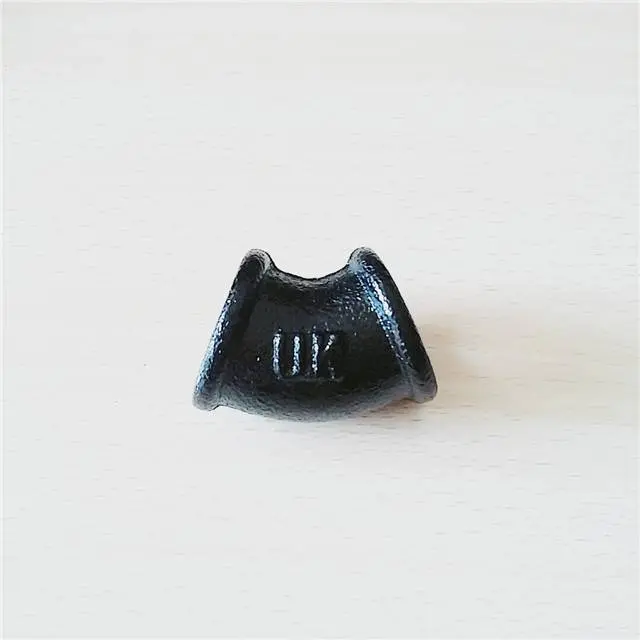
This step is critical, as it ensures the flange's compatibility with mating parts and meets the required tolerances This step is critical, as it ensures the flange's compatibility with mating parts and meets the required tolerances
flange dn20 factory.
Next comes the drilling process, where holes are precisely drilled to accommodate bolts that will secure the flange to the pipe or equipment. These holes must align perfectly with those on the mating flange to ensure a leak-proof seal. The flange is then subjected to non-destructive testing, such as ultrasonic or radiographic inspection, to detect any defects that could compromise its integrity.
Quality control is a fundamental aspect of a flange DN20 factory. Each flange is meticulously inspected at every stage of production, adhering to international standards like ANSI (American National Standards Institute), ASME (American Society of Mechanical Engineers), or DIN (Deutsches Institut für Normung). These standards dictate not only the design but also the material specifications, dimensions, and pressure ratings, ensuring safety and reliability.
Upon successful completion of all tests and inspections, the flanges are coated to prevent corrosion and then packaged for shipment. A reputable flange DN20 factory understands the importance of timely delivery, often maintaining a stock of standard flanges to cater to urgent customer needs.
In conclusion, the production process at a flange DN20 factory is a testament to the meticulousness and precision required in manufacturing these essential components. From selecting the right materials to stringent quality checks, every step contributes to the reliability and safety of the final product. These factories are the backbone of countless industries, ensuring efficient and secure piping connections that keep our world running smoothly.